How To Apply Cstr Design? Easy Guide
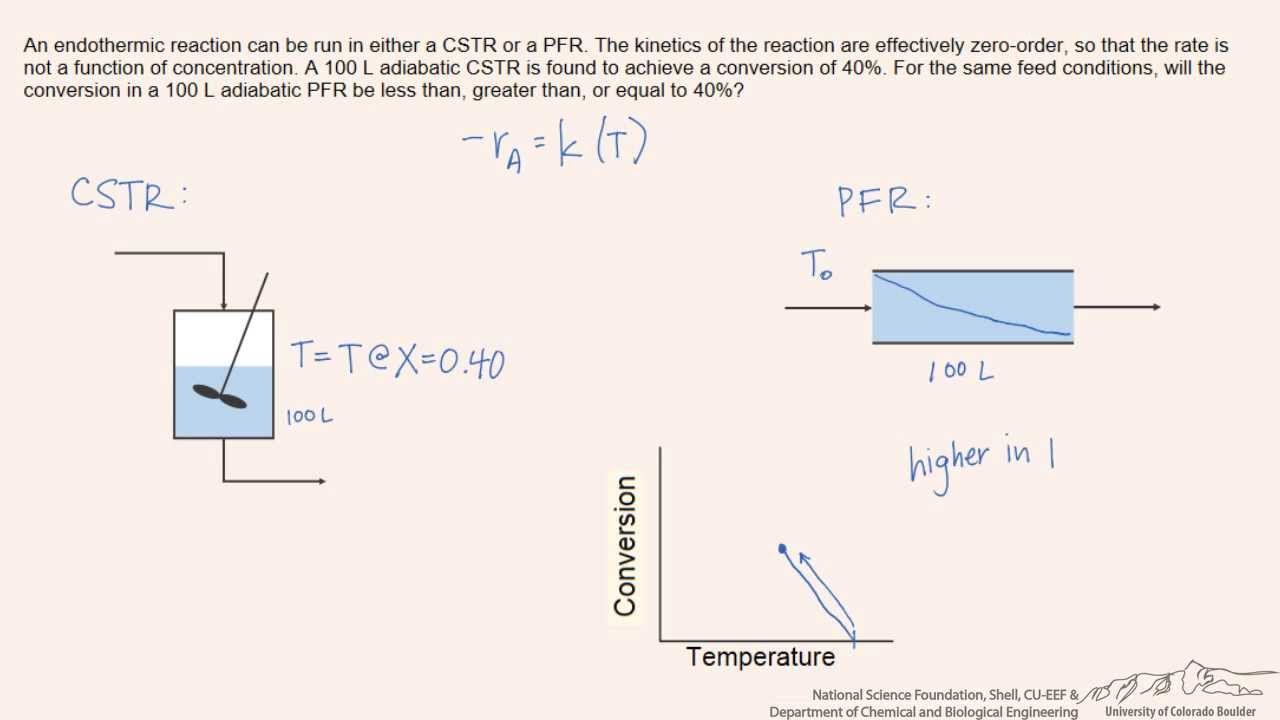
Continuous Stirred Tank Reactor (CSTR) design is a critical aspect of chemical engineering, particularly in the development of processes that involve chemical reactions. A CSTR is a type of reactor that operates by continuously adding reactants and removing products, allowing for a consistent reaction rate and product quality. Applying CSTR design effectively requires a thorough understanding of the underlying principles and factors that influence its performance.
Understanding the Basics of CSTR
Before diving into the design process, it’s essential to grasp the fundamental principles of a CSTR. This type of reactor is characterized by its continuous operation, where reactants are fed into the reactor, and products are withdrawn at the same rate, maintaining a constant volume. The key features of a CSTR include:
- Agitation: To ensure uniformity in concentration and temperature throughout the reactor.
- Continuous Feed and Discharge: Reactants are continuously fed into the reactor, and products are continuously withdrawn.
- Constant Volume: The volume of the reaction mixture remains constant due to the balanced feed and discharge rates.
Steps in CSTR Design
The design of a CSTR involves several steps, each critical to ensuring the reactor operates efficiently and safely.
1. Define the Reaction
Understanding the chemical reaction that will occur in the CSTR is paramount. This includes knowing the reactants, products, reaction kinetics, and any side reactions. The stoichiometry of the reaction helps in calculating the required feed rates and reactor volume.
2. Determine the Reaction Rate
The reaction rate equation is crucial for designing the CSTR. It helps in calculating the required residence time (the time the reactants spend in the reactor) for a given conversion. The reaction rate is typically expressed in terms of the concentrations of the reactants and catalysts (if any).
3. Choose the Operating Conditions
Operating conditions such as temperature, pressure, and feed concentrations significantly affect the reaction rate and equilibrium conversion. These conditions must be optimized to achieve the desired product yield and selectivity while minimizing energy consumption and potential hazards.
4. Calculate the Reactor Volume
The volume of the CSTR can be calculated using the formula:
[ V = \frac{F}{r} ]
Where: - ( V ) is the volume of the reactor, - ( F ) is the feed rate of the limiting reactant, - ( r ) is the reaction rate per unit volume.
5. Design the Agitation System
Proper agitation is necessary to ensure that the reactants are well mixed, which is crucial for achieving uniform reaction rates throughout the reactor. The design of the agitation system, including the type and size of the agitator, depends on the reactor size, viscosity of the reaction mixture, and desired level of mixing.
6. Consider Heat Transfer
Many chemical reactions are exothermic or endothermic, requiring the removal or addition of heat to maintain the optimal reaction temperature. The design must include an appropriate heat transfer system, such as a jacket or coil, to control the temperature within the reactor.
7. Material Selection and Construction
The materials used for the construction of the CSTR must be compatible with the reactants and products to prevent corrosion and contamination. The reactor design must also comply with safety and regulatory standards.
Example of CSTR Design
Let’s consider a simple example of designing a CSTR for the reaction A → B, where the reaction rate is given by ( r = k \cdot [A] ), with ( k = 0.1 ) min(^{-1}). If the feed rate of A is 100 mol/min, and we want to achieve 90% conversion of A, we can calculate the required reactor volume.
Given that the feed concentration of A is 1 mol/L, and assuming a first-order reaction, the reaction rate ( r ) can be expressed as ( r = k \cdot [A] ). To achieve 90% conversion, the outlet concentration of A would be 0.1 mol/L (10% of the feed concentration).
Using the formula for the volume of a CSTR for a first-order reaction:
[ V = \frac{F \cdot (C{A0} - C{A})}{k \cdot C_{A}} ]
Where: - ( F ) is the feed rate (100 mol/min), - ( C{A0} ) is the inlet concentration of A (1 mol/L), - ( C{A} ) is the outlet concentration of A (0.1 mol/L), - ( k ) is the rate constant (0.1 min(^{-1})).
Substituting the values:
[ V = \frac{100 \cdot (1 - 0.1)}{0.1 \cdot 0.1} = \frac{90}{0.01} = 9000 \, \text{L} ]
Therefore, the required volume of the CSTR would be 9000 liters to achieve 90% conversion of reactant A under the given conditions.
Conclusion
Designing a CSTR involves a comprehensive approach, considering the reaction kinetics, operating conditions, and physical design of the reactor. By following the outlined steps and considering the specific requirements of the chemical reaction, engineers can design efficient and safe CSTRs for various industrial applications. Continuous stirred tank reactors play a vital role in chemical engineering, offering a reliable method for continuous production with consistent product quality.
FAQ Section
What is the primary advantage of using a CSTR in chemical reactions?
+The primary advantage of a CSTR is its ability to maintain a consistent reaction environment, which leads to uniform product quality and easier control over reaction conditions compared to batch reactors.
How does the agitation system affect the performance of a CSTR?
+Proper agitation in a CSTR ensures that the reactants are well mixed, which is crucial for achieving uniform reaction rates throughout the reactor. Inadequate mixing can lead to variations in product quality and yield.
What factors should be considered when selecting materials for the construction of a CSTR?
+The materials used for constructing a CSTR must be compatible with the reactants and products to prevent corrosion and contamination. Additionally, considerations must be given to durability, ease of cleaning, and compliance with safety and regulatory standards.